Building Success | Why Quality Is Key in Construction
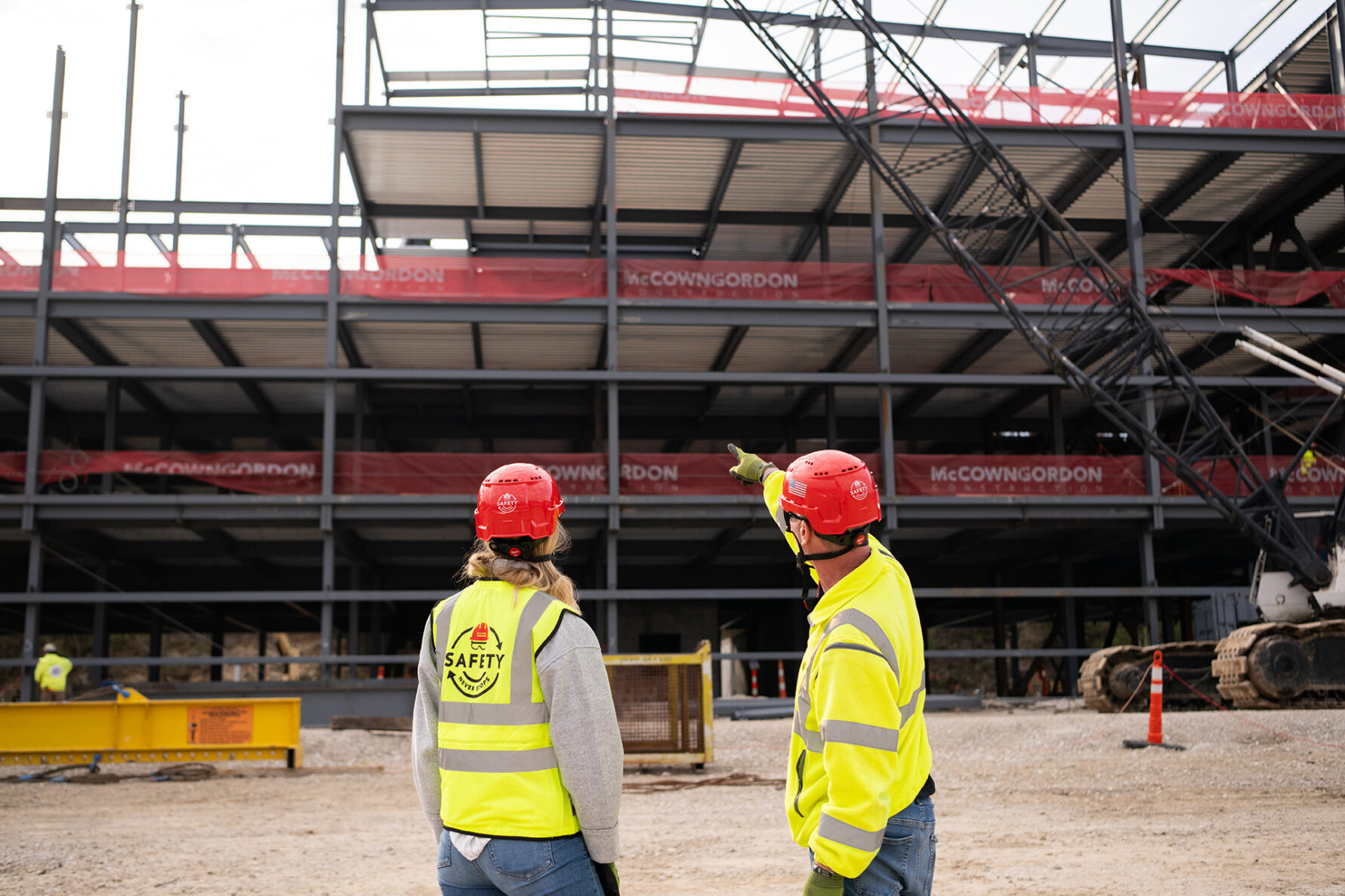
For the success of any construction project, quality plays a critical role at every phase. When choosing a general contractor to bring your vision to life, prioritize one that integrates quality into every step of the process.
Quality assurance and control are at the core of everything McCownGordon does, shaping how we manage our projects from start to finish. For us, achieving optimal outcomes is rooted in one of our core values—performance. Delivering our best means upholding our highest standards, without compromise.
McCownGordon has multiple layers to ensure that the highest level of quality is upheld during every project. Our Building Performance Solutions (BPS) group, specifically the Building Envelope and Enclosure team, manages and oversees quality, while our onsite field operations teams execute the process.
Keep reading to learn the components of quality and how McCownGordon integrates it seamlessly into every stage of our process.
What is quality assurance?
Quality assurance (QA) in construction is a systematic process to ensure that construction projects:
- Reach the useful needs of the end user
- Meet the required intent and specified standards of the design professionals
- Comply with requirements of product manufacturers installation guidelines
In short, QA is establishing the overall parameters of the construction process and setting those standards.
What is quality control?
Quality control (QC) in construction is the process of ensuring that the final product meets the specified standards and requirements established during the QA phase. A few ways this is done is through:
- Material verification
- Periodic inspection
- Testing
Briefly put, QC measures the work product(s) in construction and comparatively analyzes the product to determine if it is meeting the standards.
Our approach to quality
One of McCownGordon’s key differentiators when it comes to quality is our BPS group, a multidisciplinary team dedicated to enhancing project quality and efficiency. The group consists of six specialized teams: Mechanical, Electrical and Plumbing (MEP); Structural Engineering; Virtual Design and Construction (VDC); Commissioning (Cx); Sustainability; and Building Envelope and Enclosure. While the Building Envelope and Enclosure team is dedicated to ensuring quality, every team plays a crucial role in delivering a high-quality final product.
Our BPS team engages early—well before a project is awarded—bringing depth of knowledge and meticulous attention to detail that positions McCownGordon for success. Once the project is underway, the team seamlessly integrates through every phase, from preconstruction and construction to commissioning and closeout, ensuring excellence at every step.
BPS provides a comprehensive range of services and expertise, each enhancing the level of project quality:
The Mechanical, Electrical and Plumbing (MEP) collaborates with the estimating team to validate budgets and analyze cost options, ensuring alignment with the owner’s goals. In the construction phase, they observe installations, create non-compliance reports and help resolve field issues to ensure the final product performs as intended.
Our Structural and Soils group also assists early with system substantiation and value propositions. The team additionally collaborates on developing bid packages and interviewing specialty trade partners. In the construction phase, they observe installations, review special inspection discrepancies and aid in resolving issues in the field.
Our Virtual Design and Construction (VDC) experts use advanced digital tools like 3D models and virtual mockups to add value throughout the entire project timeline, reducing cost, time and waste, while improving efficiency and quality. They are also the team responsible for all of the technology we use in our construction operations such as aerial photography, 360 photography, laser scanning and augmented reality (AR).
The Building Commissioning (Cx) team improves energy efficiency, reduces operational costs, and sets up the owner, building, and maintenance team for long-term success. They achieve this by helping to the owner establish measurable goals, evaluate design documents for adherence to those goals, and testing systems and equipment to verify their performance. All of those results and operator trainings are documented for future reference. Our in-house team ensures a more streamlined and objective process.
Our Building Envelope and Enclosure group evaluates the systems that separate a building’s interior from the exterior. We focus on four key control layers—water, air, vapor and thermal—ensuring proper interfacing, sequencing, material compatibility and long-term durability during construction. They, too, observe installations, create non-compliance reports and help resolve field issues to ensure the final product performs as intended.
The Sustainability team performs site and building evaluations to reduce construction’s environmental impact. We evaluate energy usage versus utility, maintenance and replacement costs to provide client’s the most sustainable option.
Importance of quality
Quality is the cornerstone of all successful projects. A strong quality plan not only ensures excellence in construction but also sets the standard for building it right the first time. Every aspect of a construction project hinges on the quality plan outlined in the contract, keeping quality a top priority from start to finish. Without it, issues such as defects, shortened building lifespan, miscommunication and costly changes can arise. By prioritizing quality from the outset, you create a foundation for long-term success.
Additionally, quality and cost control go hand in hand. By implementing advanced planning and establishing clear quality standards from the start, we minimize the risk of costly errors during construction, ensuring a more efficient and financially sound project.
Prioritizing quality not only enhances a project’s success but also improves safety. Defects and failures aren’t just costly—they can create hazardous conditions, often requiring trade partners to redo work in less-than-ideal environments. Many accidents are preventable through attention to detail and a commitment to getting the job done right the first time. When everyone is aligned in a quality-driven environment from the start, the risk of accidents decreases significantly.
Ultimately, quality ensures the best possible outcome. No one wants to invest time and resources into a construction project only to end up with mediocre results. At McCownGordon, our dedication to quality sets us apart, ensuring that every build meets the highest standards. While cutting corners may seem faster, true success in construction comes from a strong foundation of quality—because in the end, it’s what makes or breaks a project.
Quality control in preconstruction
During preconstruction, our dedicated BPS team, in combination with the operations team, analyze every detail of the construction project to develop a tailored quality approach for the site. From there, we build checklists and guidelines for each process, including design, safety and managing trade partners. Our team uses constructability reviews to ensure systems are designed to be practical, maintainable and aligned with project goals. By identifying potential construction challenges early and assessing feasibility, we help prevent costly delays and ensure smooth project execution. This proactive approach yields well-coordinated installations and higher-quality outcomes, ultimately saving time and costs.
BPS is instrumental in elevating quality during the preconstruction phase. Our VDC team utilizes advanced clash detection to proactively resolve spatial conflicts beween mechanical, electrical, plubming, fire protection, structural and architectural components. Our MEP specialists conduct thorough verifications to minimize rework and delays. Additionally, our in-house structural and envelope specialists perform comprehensive scope reviews and drawing assessments to ensure precision, cross discipline and trade coordination, and alignment with project requirements.
Since McCownGordon is actively involved in every community we build in, we have the unique capability of knowing which trade partners will work best for your unique project. As a result, we can help owners choose trade partners who can uphold our high standards. While we strive to give our clients the most value, we also want to ensure our trade partners don’t compromise quality for the sake of saving money.
The key to success is establishing clear and open communication during preconstruction, laying a strong foundation for the rest of the construction process. When clients, designers, and trade partners have a clear understanding of quality standards from the start, it leaves less room for error and confusion later in the project. As a bonus, communication leads to more engagement, which can greatly improve the efficacy and speed of a project.
McCownGordon’s quality control process
Guided by our commitment to “Deliver the Best Building Experience,” our team goes above and beyond to ensure exceptional quality, resulting in durable, long-lasting builds. Our attention to detail minimizes changes during the construction process, ensuring a smoother project.
Our BPS team’s main priority is ensuring everyone involved with a project keeps our standards at the forefront. Through the use of our innovative technology, strict enforcement and persistent follow-up, our team keeps clients at peace knowing we are not only meeting expectations but exceeding them.
During the construction of your project, we will go through three phases to ensure high quality.
Phase 1: Pre-installation
The pre-installation phase starts at the beginning of each major scope of work. Our team will conduct pre-installation meetings with the design team, owner, project management team, superintendent, trade contractors and anyone else involved in the project. These meetings include:
- Shop drawing review
- Detailed schedule review
- Trade partner coordination
- Coordination with existing conditions
By establishing the expected level of quality at the start of a project, we’re able to streamline those expectations all the way until post construction.
Phase 2: Installation
Once construction crews are ready to start, it’s time to move into the installation phase. Our superintendent, project management team and dedicated quality control manager work closely with the trade contractor responsible for construction.
To verify that all aspects of work meet our quality control guidelines, we may:
- Create mock-up and sample comparisons
- Coordinate with the proper inspection agencies
- Implement early reviews by design team members and other consultants
As a result, we can determine whether or not each person involved with the construction process has a full understanding of our quality protocols.
Phase 3: Post-Installation
During the post-installation phase, our field operations team conducts weekly check-ins until the construction project is complete. The field operations team uses these weekly reports to develop a comprehensive quality control checklist, ensuring thorough documentation of the process and compliance of the work in place. At the end of the day, we don’t want to guess everyone is on the same page with quality, we want to know, without a doubt, that trade partners and other contractors are doing everything they can to meet expectations.
Keep in mind all projects can and will change. Therefore, we are always adapting our site-specific quality plan to adjust to changes. For example, we may have to revisit and adjust planning and coordination items that we set in place during the pre-installation phase to maintain a high level of quality. Remember, quality is a proactive culture, meaning you should expect your general contractor to remain flexible and always think of ways to enhance a project.
At McCownGordon, our goal is to have zero punch-list items prior to the final punch-list. During construction of each project, we perform the required tests to make sure everything is up to par. Once the project is completed, our team will ensure that everything in the building is functioning properly.
McCownGordon offers commissioning services that can begin at project conception and continue through turnover and beyond, ensuring systems and equipment function correctly and cohesively at every stage. As an owner’s advocate, our Cx team takes an operations and maintenance perspective to optimize performance and efficiency while ensuring the owner’s requirements are met. With our in-house team, clients benefit from a more streamlined and objective process.
When implemented the right way and enforced with continuous inspections, assessments, data collection, feedback and deficiency tracking, our quality control process eliminates confusion and ensures construction continues according to plan.
Want to learn more about McCownGordon?
At McCownGordon, our customers aren’t simply another project; they’re an extension of our team and community. Together, we don’t just build—we bring creative visions to life. From first thought to final nail, we are committed to delivering exceptional quality, ensuring our work stands above the rest.
We have four regional offices—Kansas City, Manhattan, Wichita and Dallas and a national manufacturing business unit. Call us at 888-304-4929 or use our free online quote tool to enhance the quality of your construction project today.