Enhanced project delivery to meet your objectives
Providing unmatched performance with commissioning
The commissioning process (CxP) ensures we meet your expectations throughout your project.
McCownGordon highly recommends involving commissioning in your project for access to its wide array of benefits and short payback timelines. CxP validates and documents that systems are in working condition to meet owner expectations. There are four primary types of commissioning: Building Commissioning, which focuses on new and retro/existing structures; Process Commissioning, aimed at ensuring all documentation has been completed to show that construction process aspects have been tested and verified functional; Packaging Commissioning, to make sure your packaging plant is ready to operate starting day one; and Equipment Startup, which involves taking equipment from inactive to active status before starting trial operation and testing.Â
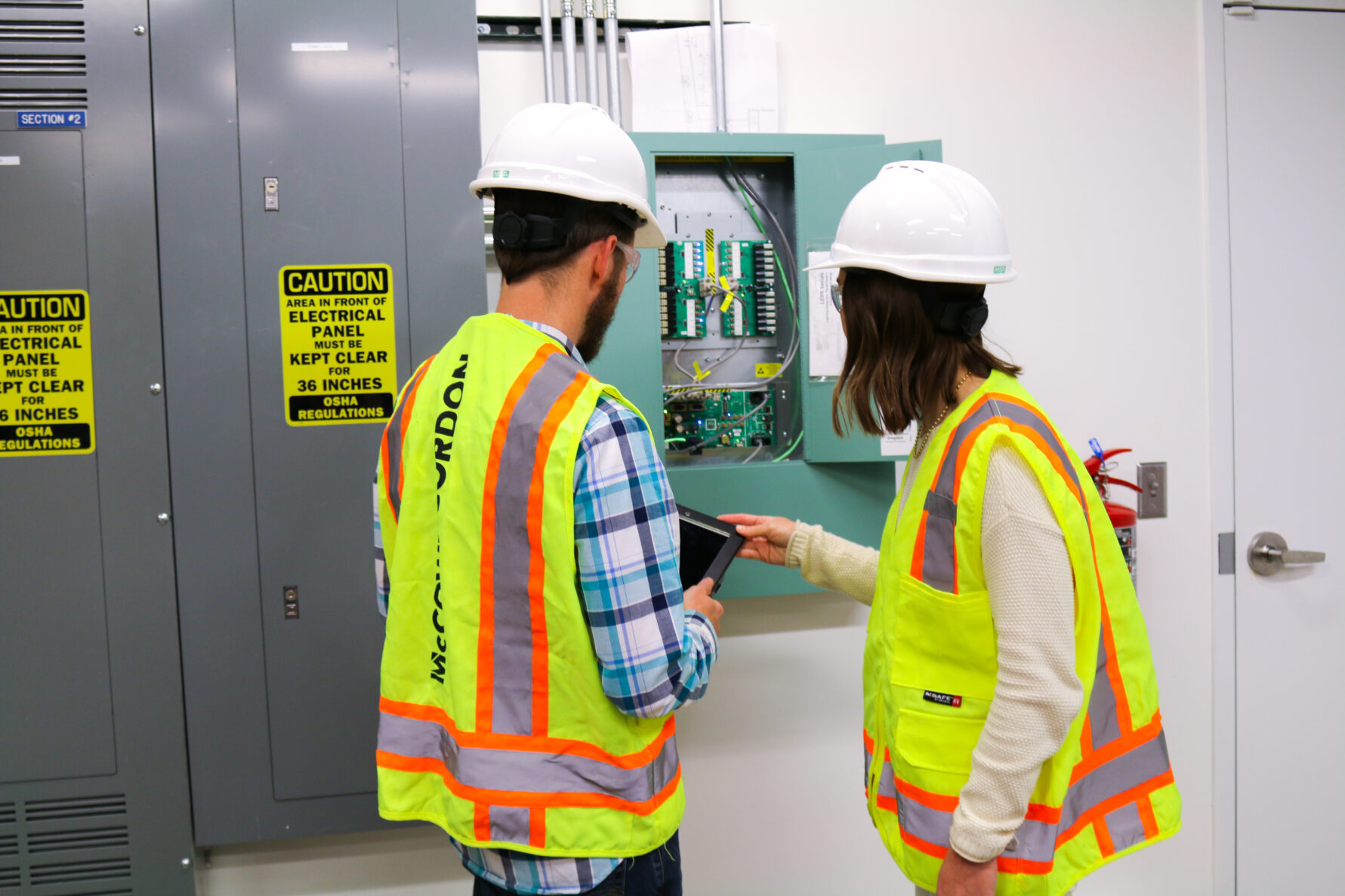
NEW BUILDING COMMISSIONING
When building a new facility, or retrofitting an existing one, commissioning provides a systemic quality assurance process that ensures all the building systems, from electrical and plumbing to heating and ventilation, from equipment functionality to trial operation testing, work as intended before people move in. The goal is to guarantee that the facility operates efficiently, safely, and in line with its design.Â
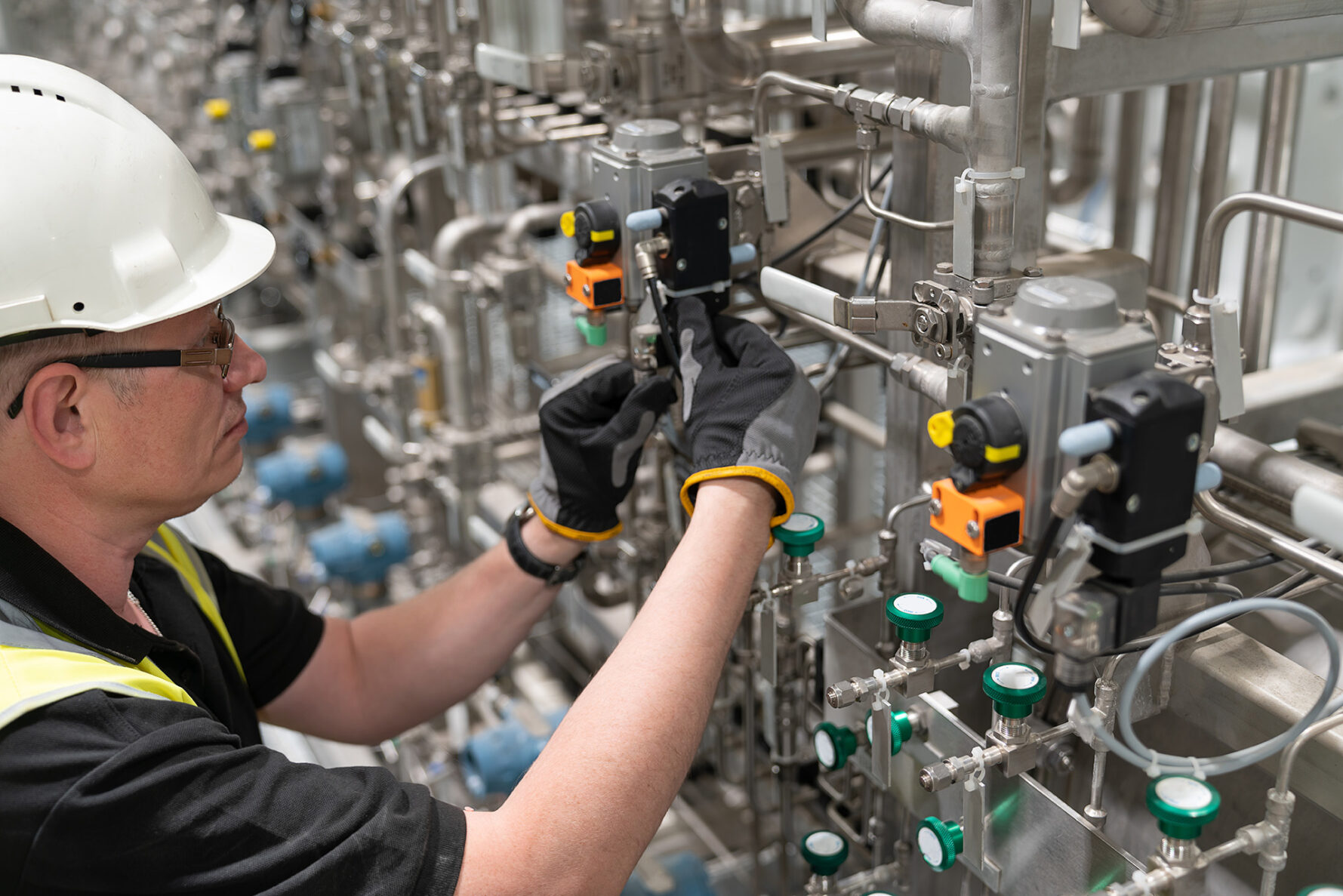
PROCESS COMMISSIONING
Process commissioning ensures that systems and equipment function efficiently and meet design specifications. It involves rigorous testing, inspection, and verification of mechanical, electrical, and control components before a facility becomes operational. This critical phase identifies and rectifies potential issues, ensuring a smooth transition from construction to functional operation for your facility.
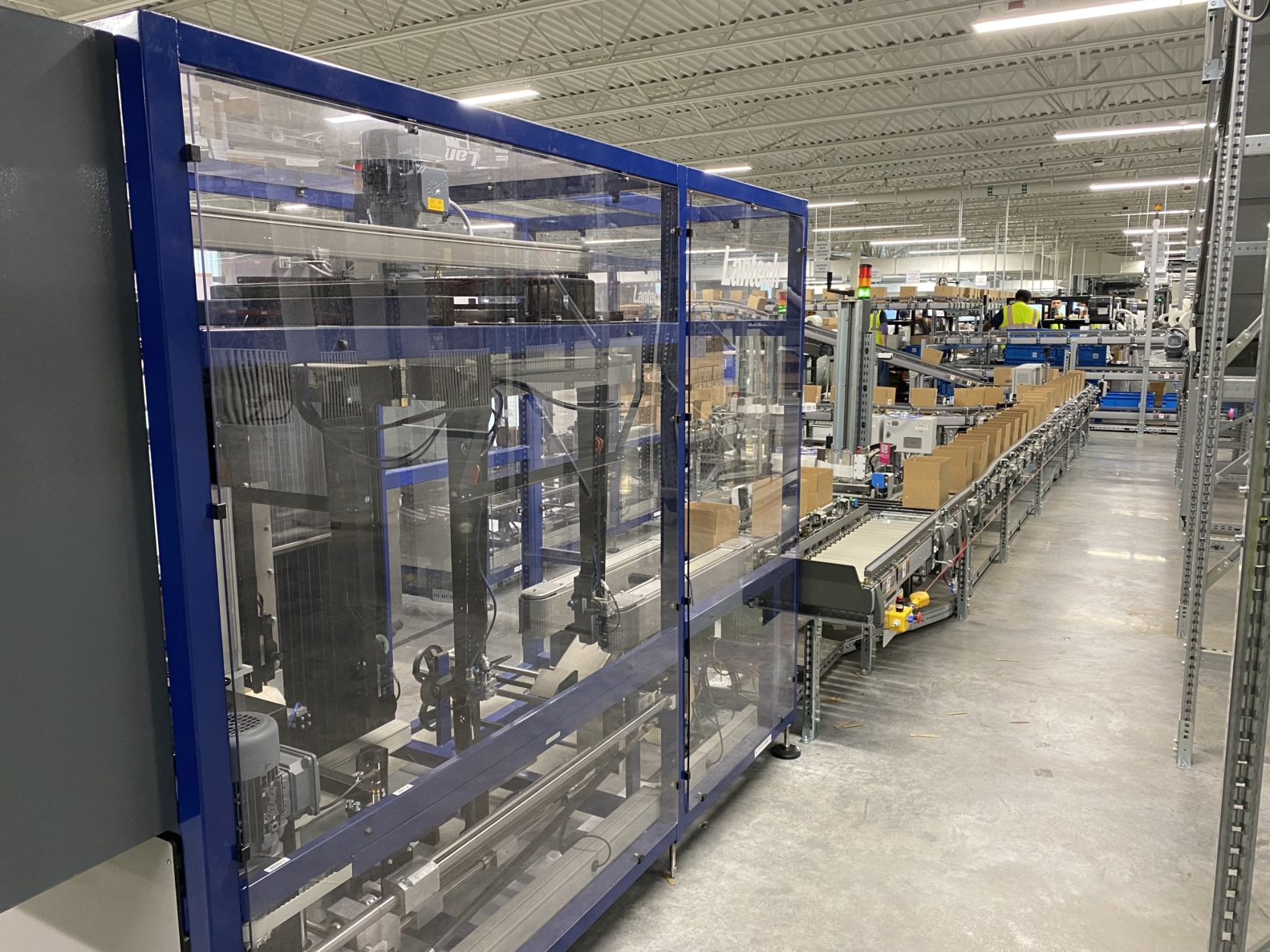
PACKAGING COMMISSIONING
Packaging commissioning tests and certifies the functionality of packaging systems within facilities. It ensures that equipment such as conveyor systems, labeling machines, packaging lines, etc., operate according to specifications. This process focuses on optimizing efficiency, identifying potential issues, and guaranteeing that the packaging components integrate seamlessly within the overall construction project, facilitating a successful operational transition.
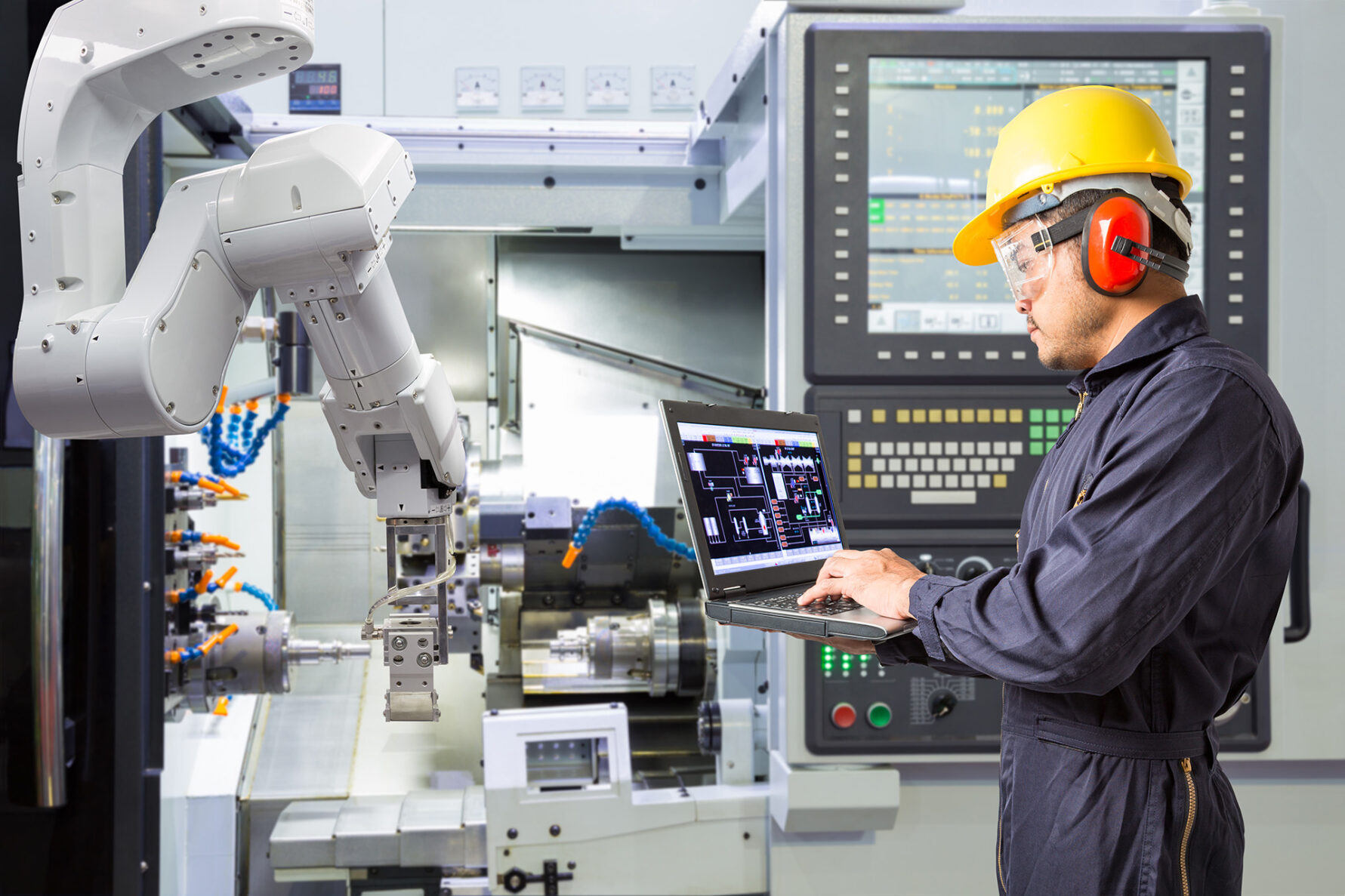
EQUIPMENT START-UP
McCownGordon’s equipment start-up involves the initiation and testing of machinery and systems to ensure proper functionality. This crucial phase verifies that each component operates according to design specifications, identifying and addressing any issues before full-scale operation. It plays a pivotal role for your manufacturing facility, ensuring that equipment is ready for optimal performance prior to trial operation and testing.
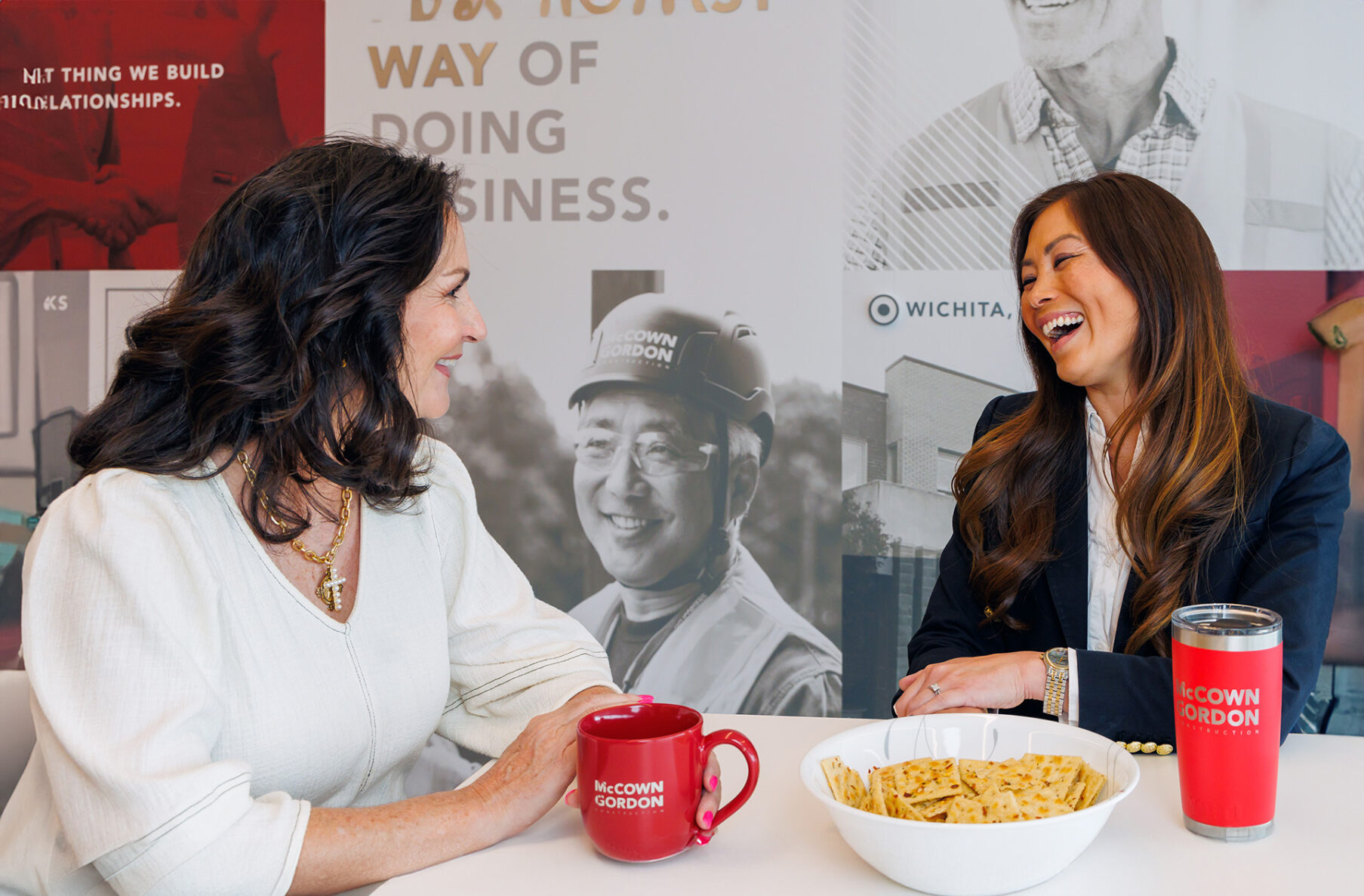
The first thing we build is relationships.
Use our Manufacturing Project Planning Tool to get started.