Driving Efficiency with the Rapid Evolution of Laser Scanning
Introducing the NavVis VLX 3 Scanner

When it comes to complex design and construction projects, performing a laser scan of an existing site or facility to capture detailed as-built data and conditions is crucial. McCownGordon leverages the latest scanning technology including Simultaneous Localization and Mapping (SLAM) scanning. SLAM scanning differs from traditional terrestrial scanning in that the scanning device is carried or worn by the person conducting the scan, as opposed to setting up the device in a stationary position on a tripod at various points throughout a space.
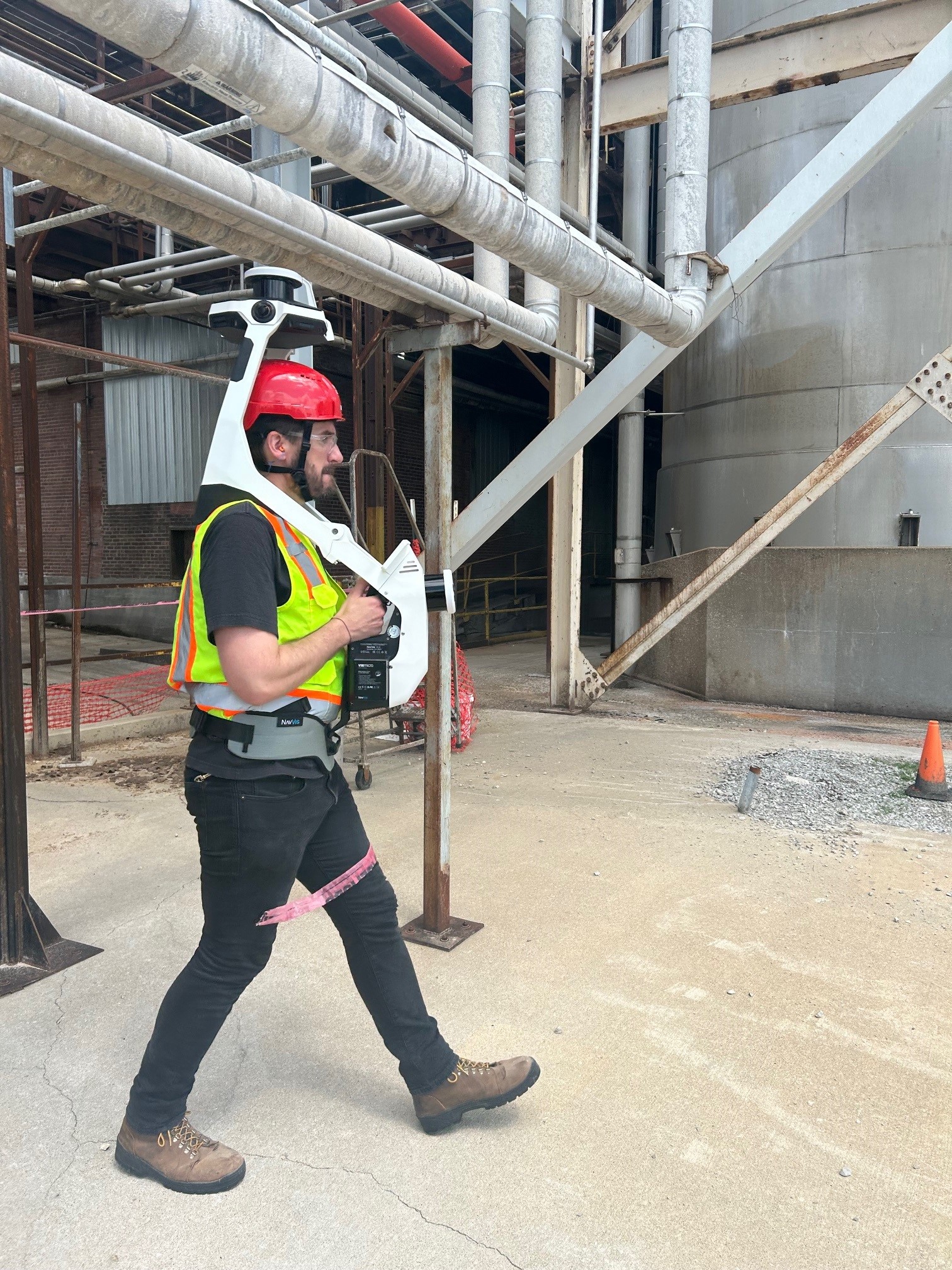
High-definition surveying, sometimes referred to as laser scanning or 3D scanning, is the process of collecting millions of survey points that are measured by quantifying the time it takes light to leave the scanner, reach a point, and return to the device, thus registering as a precise distance. The typical deliverable from laser scanning is a 3D point cloud model, which is then used to develop precise models, which is often used for complex renovation work. This information reduces cost and time for both the design and construction phases, while improving efficiency and quality. The downside? Historically, this process has been known to take weeks or even months.
What was once a time-consuming and labor-intensive effort to document as-built conditions with a traditional (terrestrial) laser scanner is now a quick and seamless process. McCownGordon recently acquired a NavVis VLX 3 scanner, a state-of-the-art wearable (SLAM) mobile mapping system designed for capturing high-quality, detailed reality capture data for complex sites, both indoor and outdoor.
Our in-house Virtual Design and Construction (VDC) team recently leveraged the technology at a biofuel production facility and scanned the entire project in less than an hour! Over 85,000 square feet of complex space was scanned, including platforms, walkways, and stairs accessing the primary stacks. Using a terrestrial scanner would have likely taken two or three days to collect the same data, and challenges would have been encountered in tight spaces around piping, tanks, and other obstructions due to the tripod setup method and space limitations. Data would have likely been omitted or inaccurate in some hard-to-reach locations. Once the scan data was processed, a 3D point cloud model was shared with the design team, which allowed them to develop a fully coordinated design model in a matter of days compared to weeks.
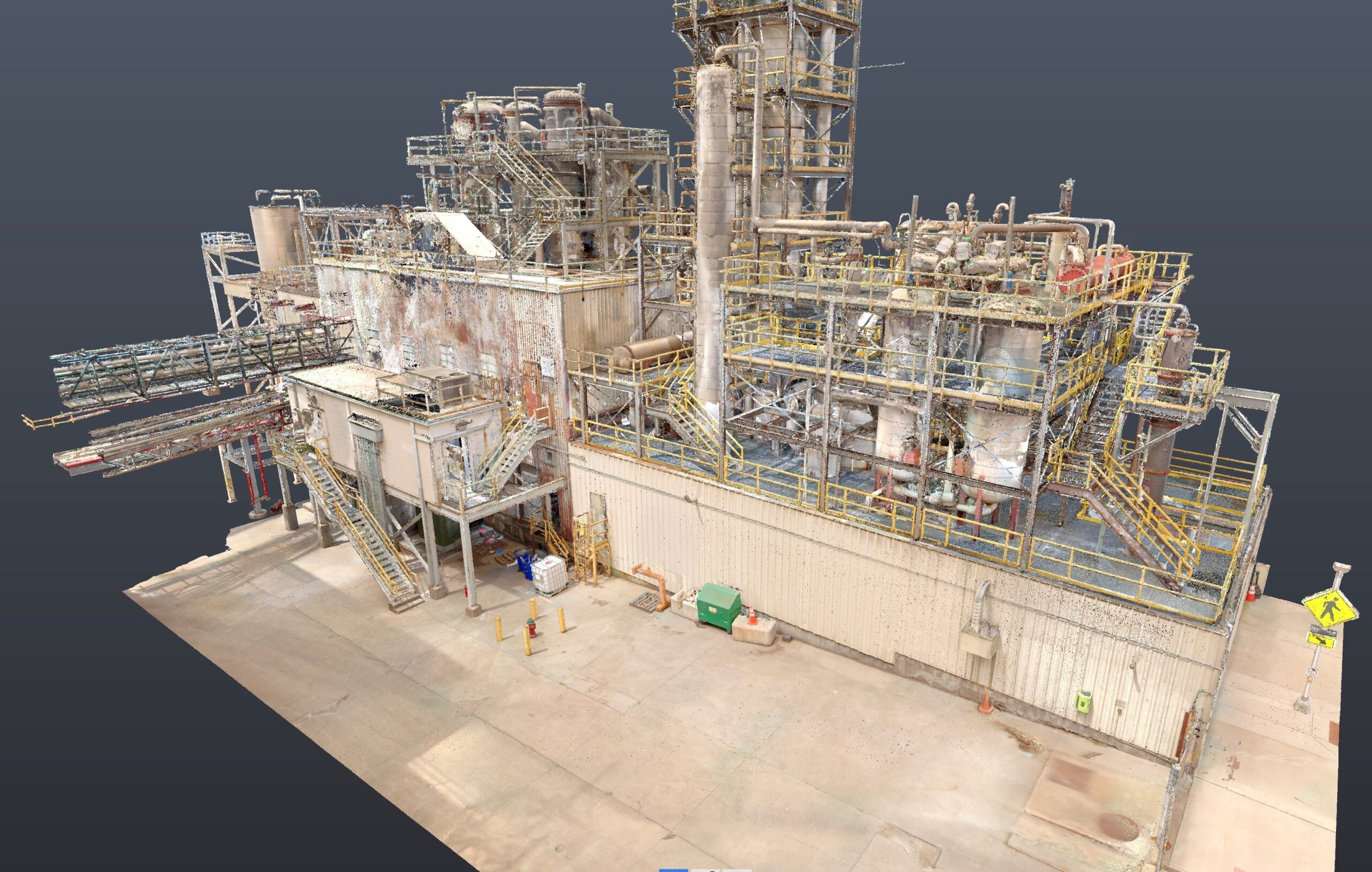
Utilizing the model data, McCownGordon adds increased value throughout the design, preconstruction, and construction process. Having access to more accurate and higher quality design models streamlines the efficiency and accuracy of 3D coordination during construction. The increased collaboration allows owners, architects, engineers, and trade partners to communicate using highly accurate data, which in turn assists teams in making the most informed decisions for project success, all while reducing risk. Leveraging the latest cutting-edge technology, McCownGordon maximizes the information available to our clients, which ultimately results in budget and schedule savings.
“Partnering with McCownGordon on our biofuel expansion project has been a game-changer. During preconstruction, they introduced the latest laser scanning technology, providing us with an accurate picture of the existing facility down to the millimeter. This approach, which also incorporated 3D photography, significantly enhanced our existing facility’s documentation, and helped us visualize how the new equipment fit into the space. Their proactive planning and innovative ideas saved us an incredible amount of time. McCownGordon streamlined the design process, resulting in substantial time and cost savings. We couldn’t be happier with the results!” – Matt Greeno, Corp. Director of Engineering, MGP